Labeling Methods for Tissue and Implant Tracking Software.
Two methods for labeling tissue.
Different approaches to labeling in tissue and implant tracking software can have a major impact on hospital operations. The Joint Commission Tissue Standards require healthcare organizations to track all tissue handling from the moment tissue items enter the facility until they are used by patients or disposed of. Hospitals must establish a system that ensures the traceability of all tissues and implement procedures for investigating and reporting adverse events. A system that tracks the source of the tissue, the condition at arrival, the temperature at storage, the movement from one department to another, the return to the supplier, expired tissue on shelves, and the ability to identify patients in the event of a recall typically requires tissue and implant tracking software.
Different labeling methods can directly affect hospital operations. Labeling can either simplify or complicate routine processes when entering tissue items into inventory. The use of an effective labeling strategy ensures efficient inventory management and streamlines clinical and supply chain workflows, reducing this laborious task for OR nurses, tissue coordinators, and other healthcare personnel.
Different labeling methods can directly affect hospital operations. Labeling can either simplify or complicate routine processes when entering tissue items into inventory. The use of an effective labeling strategy ensures efficient inventory management and streamlines clinical and supply chain workflows, reducing this laborious task for OR nurses, tissue coordinators, and other healthcare personnel.
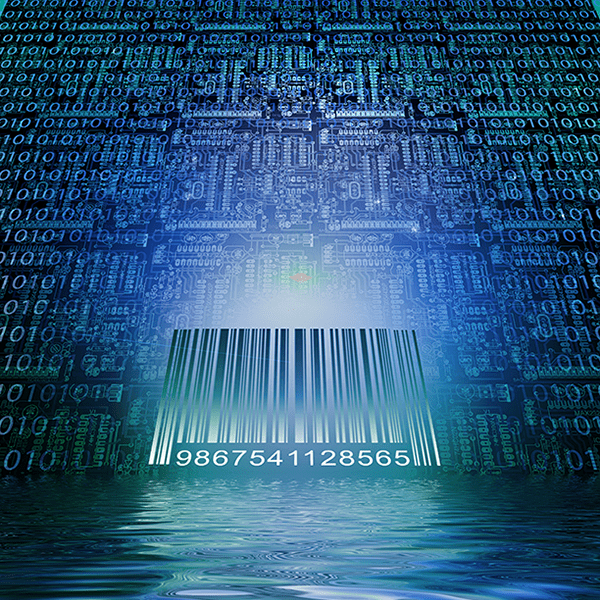

Two methods for labeling tissue.
Different approaches to labeling in tissue and implant tracking software can have a major impact on hospital operations. The Joint Commission Tissue Standards require healthcare organizations to track all tissue handling from the moment tissue items enter the facility until they are used by patients or disposed of. Hospitals must establish a system that ensures the traceability of all tissues and implement procedures for investigating and reporting adverse events. A system that tracks the source of the tissue, the condition at arrival, the temperature at storage, the movement from one department to another, the return to the supplier, expired tissue on shelves, and the ability to identify patients in the event of a recall typically requires tissue and implant tracking software.
Different labeling methods can directly affect hospital operations. Labeling can either simplify or complicate routine processes when entering tissue items into inventory. The use of an effective labeling strategy ensures efficient inventory management and streamlines clinical and supply chain workflows, reducing this laborious task for OR nurses, tissue coordinators, and other healthcare personnel.
Different labeling methods can directly affect hospital operations. Labeling can either simplify or complicate routine processes when entering tissue items into inventory. The use of an effective labeling strategy ensures efficient inventory management and streamlines clinical and supply chain workflows, reducing this laborious task for OR nurses, tissue coordinators, and other healthcare personnel.
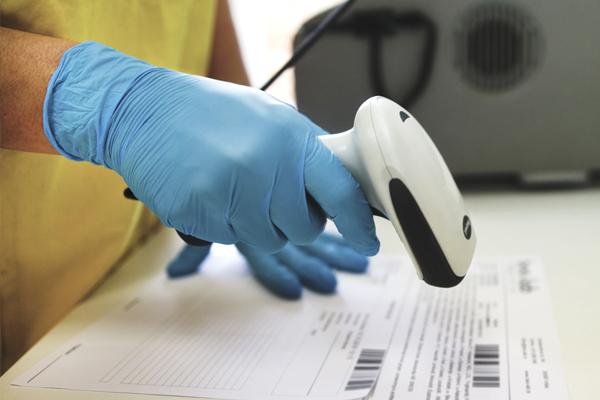
Method 1: Scan the existing tissue manufacturer's barcode.
Scan the existing manufacturer’s barcode. There is no need to re-label tissue products. InVita prefers this method as it is simple and effective to minimize the time and effort involved in receiving items into inventory. With the ability to scan, read, and parse GS1 Barcodes, relevant data can be captured quickly and accurately, which is then automatically entered into software. Not only is it a time-saving solution, but it also reduces potential mistakes when data is manually entered.
Method 2: Scan a tissue tracking software vendor's custom label.
Some vendors require that all tissue items bear an additional number to capture information already contained in the manufacturer’s barcode. This additional number is not provided by the manufacturer. It is not a requirement of Joint Commission, FDA, or any other compliance agency. It is only required by the tissue management software that is dependent on these additional identifiers. However, it also requires the creation of custom labels.
Every tissue item must first be identified and received into inventory to generate a custom label. This entails having hospital staff manually enter long strings of data for several fields into the tissue tracking software. Most of the manual data entry is composed of data already part of the tissue manufacturer’s barcode. When all fields of information have been entered into the system, is it possible to print a custom label and attach it to the product.
Every tissue item must first be identified and received into inventory to generate a custom label. This entails having hospital staff manually enter long strings of data for several fields into the tissue tracking software. Most of the manual data entry is composed of data already part of the tissue manufacturer’s barcode. When all fields of information have been entered into the system, is it possible to print a custom label and attach it to the product.
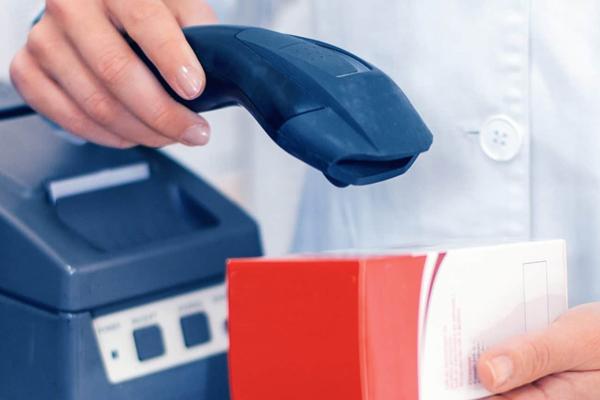
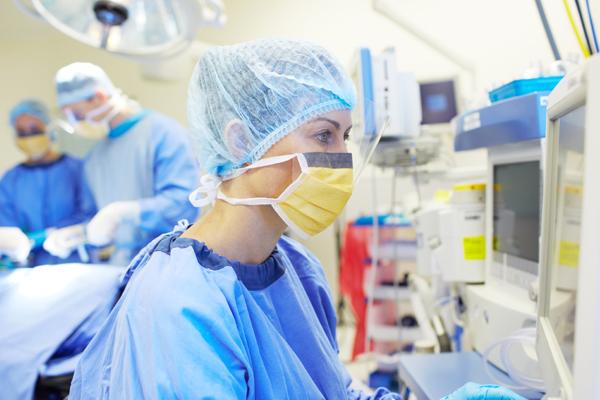
Custom labels are time consuming and not required for tissue and implant tracking.
Manual data entry to receive an item before printing a custom label may not sound like a significant time drain, but the redundant effort adds up in a hurry. One study estimated that hospital staff spend an additional 10 minutes per unit relabeling tissues when using software that required custom labels. Now consider how much time it would take to enter every item in inventory – typically thousands of items – at several minutes per item.
A custom label is not required. Adding a second label to the package makes it necessary to train hospital staff to scan the correct label.
A custom label is not required. Adding a second label to the package makes it necessary to train hospital staff to scan the correct label.
Custom labels make non-biologic implant tracking impractical.
As part of the FDA’s Unique Device Identification System final rule (UDI Rule), manufacturers’ labels are required to identify non-biologic implants and medical devices from manufacturer to patient use. These labels provide information for tracking patient safety, product recalls, and other regulatory requirements.
With over 300,000 non-biologic items on the market, hospitals are not able to carry enough inventory to cover all their needs. Many Non-biologic implants are brought in by a manufacturer’s representative on the day they are needed. Reps often bring dozens of similar items to ensure surgeons have several options at their disposal. It is simply not practical to spend several hours manually entering data to receive and relabel dozens of non-biologic items before surgery.
With over 300,000 non-biologic items on the market, hospitals are not able to carry enough inventory to cover all their needs. Many Non-biologic implants are brought in by a manufacturer’s representative on the day they are needed. Reps often bring dozens of similar items to ensure surgeons have several options at their disposal. It is simply not practical to spend several hours manually entering data to receive and relabel dozens of non-biologic items before surgery.
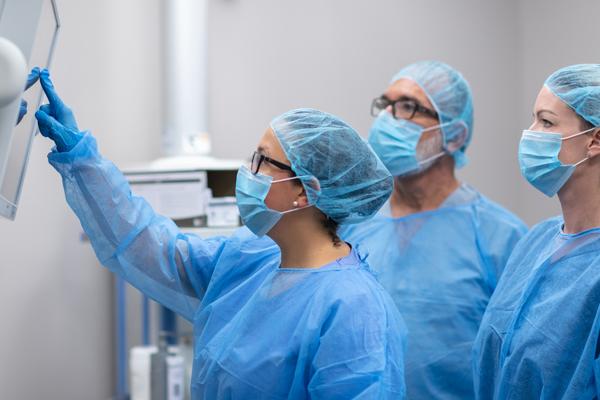
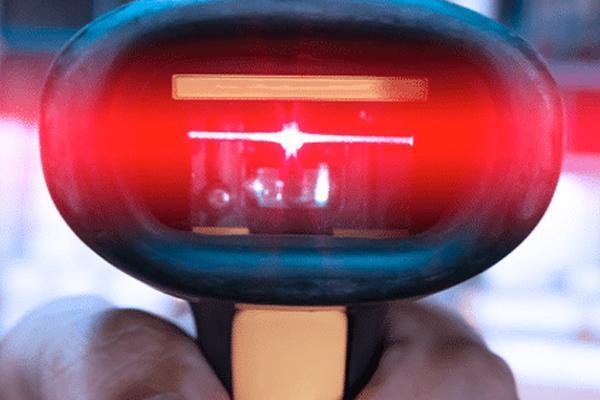
Track tissue and non-biologics with one tracking system.
With sixty percent of tissue and all non-tissue implants following the GS1 Barcode standard today, software that supports GS1 barcodes allows staff to track and manage tissue and implants quickly, easily, and cost-effectively. Using FDA-mandated labeling and manufacturer-defined identifiers, ready-to-read barcodes capture tissue or implant model number, size, batch, lot number, and expiration date – all with one single scan.
Software integrated with EHR and implant manufacturers
Software that integrates with manufacturers and allows staff to scan, read, and parse GS1 Barcodes and FDA-mandated identifiers eliminates the need to relabel products. UDITracker ® is the only software solution with GS1 Barcode capabilities, enabling staff to track and manage implants in a time-efficient manner, reducing staff burden, and ensuring accuracy and compliance while improving patient safety.
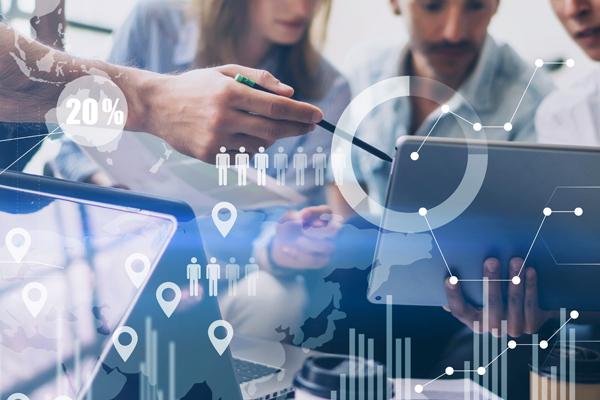